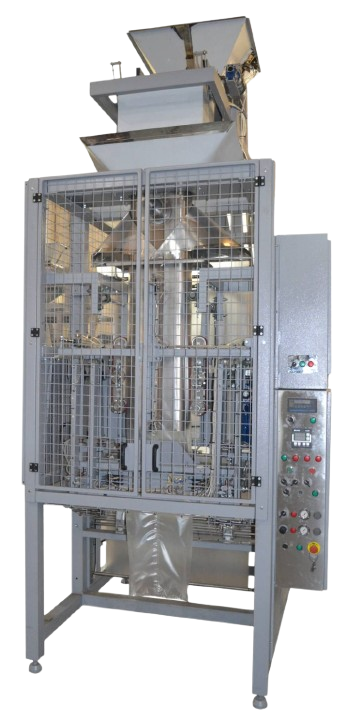
This packaging machine is designed to provide a continuous packaging cycle, weighing dosing of bulk products (fuel granules, pellets, animal feed, sand, crushed stone, salt, fertilizer) and their packaging in polyethylene (PE) or multilayer films.
The equipment consists of a vertical packaging machine and an electronic weigh batcher with a belt or vibration feeder.
The equipment allows for dosing (packaging) of bulk products from 2 to 50 kg according to a specified weight, and packaging of these products in large packages (bags).
Characteristics.
Power supply, V/Hz | 380/50 |
Power consumption, kW/hour | 3.5 |
Pneumatic supply**, atm./l.min. | 6/500 |
Length / Width / Height (not more than), mm | 2900/1800/4600 |
Weight (not more), kg | 950 |
Width/Diameter of film roll (max.), mm | 1050/500 |
Productivity (kinetic)*, packs/hour | 500 |
L/W of package (max.), mm | 700/500 |
Dosage range, g | 2,000 – 50,000 |
Volume of storage bin, l | 100 |
* Productivity depends on the weight of the dose, the length of the package, the properties of the packaging material.
** To ensure the functioning of the pneumatic drives of this packaging machine, a „compressor” is required (supplied separately).
Description of work.
The product to be packed is poured through the hopper neck onto the feeder*, with the help of which it is fed into the weighing bucket. The bucket is attached to the frame of the batcher on a strain gauge (strain gauge). Upon reaching the specified weight parameters, the load cell sends a signal to the control unit of the batcher (the Libra controller), which stops the vibrating tray, ceasing the product feed.
Upon receiving a pulse from the control unit of the packaging machine (the „Unloading” signal), the batcher controller sends a signal to open the weighing bucket*. The bucket opens, pouring its contents into the funnel. Through the funnel, through the tube of the sleeve-forming device, the product is poured into a rolled-up tube (sleeve) of packaging film with a sealed back seam and bottom (packaging blank). At this time, the controller switches on the feeder to fill the weighing bucket with the next portion of the product.
The seam of the bottom of the package is clamped in the horizontal clamps of the soldering unit, which remain compressed until the end of the dose delivery. This eliminates the pressure of the dose on the seam and the likelihood of its rupture as a result of an impact when the dose falls or when the packaging material has not cooled down from welding.
The operation of the packaging machine is controlled by a microcontroller located in the control unit, which, after unloading the weighing bucket (dispensing a dose of product), releases the clamps of the soldering unit and turns on the feeding of the packaging material. The pulling is performed using an electric motor and belts to the length set by the operator (determined by the photo mark or the value of the parameter „СЧt. 1”). During pulling, the roll is unwound and the film is rolled up through the collar into a sleeve around the tube.
Having pulled the film to the required distance, the control unit activates the soldering unit: it compresses the clamps, fixing the packaging material, and also compresses the welded elements located on the clamps and presses the vertical welded element to the tube, starting the process of welding the seams.
The soldering unit operates on the principle of constant heating, i.e. the welded elements are pressed to the packaging material for a specified time (set interval), on which the set temperature is maintained. After the specified welding time has elapsed, the welded elements are released, and the horizontal clamps remain compressed. This is necessary for cooling the packaging material and forming strong seams, which is especially important for polyethylene films, the seams of which remain flexible for a long time after welding and can break even from minor efforts. To speed up the cooling process, immediately after the welded elements are released, the control unit supplies compressed air to the nozzles located on the soldering unit and forcibly cools the formed seams (the blowing time is adjusted by the operator). The soldering unit simultaneously seals the top seam of the filled package, the bottom and back seams of the next package in one go. At the same time, at the moment of welding, the filled package is separated by cutting the packaging material with a hot „string” located on the protrusion of the horizontal welded element. At the same time, the microcontroller of the packaging machine sends a pulse to the „Libra” controller (the „Unloading” signal), filling the next package.
After the welding process is completed and the formed seams have cooled, the control unit releases the horizontal clamps and again turns on the package material feed, feeding the next filled package into the soldering unit. At the same time, the package, already sealed and cut off with a “string”, is lowered onto the discharge conveyor.
Features.
This packaging machine is optimal for packaging products that are convenient to sell in large packages (bags). Such products can be: sand, fuel granules, pellets, grain, salt, sugar, washing powder, pebbles, crushed stone, soil (not wet), compound feed, fillers for animals.
The packaging machine is not suitable for packing highly dusty products. It is necessary to take into account that due to the use of a weigh batcher, the model is universal and has no restrictions on changing the packaged product.
This device requires floor placement and has restrictions on the width of the film used and the height of the formed package, specified in the technical specifications.