CATEGORIES
Address of production facilities
Ukraine Cherkasy region, Cherkasy city
Khimikov avenue 74 D
Khimikov avenue 74 D
CATEGORIES
Integruoti sprendimai
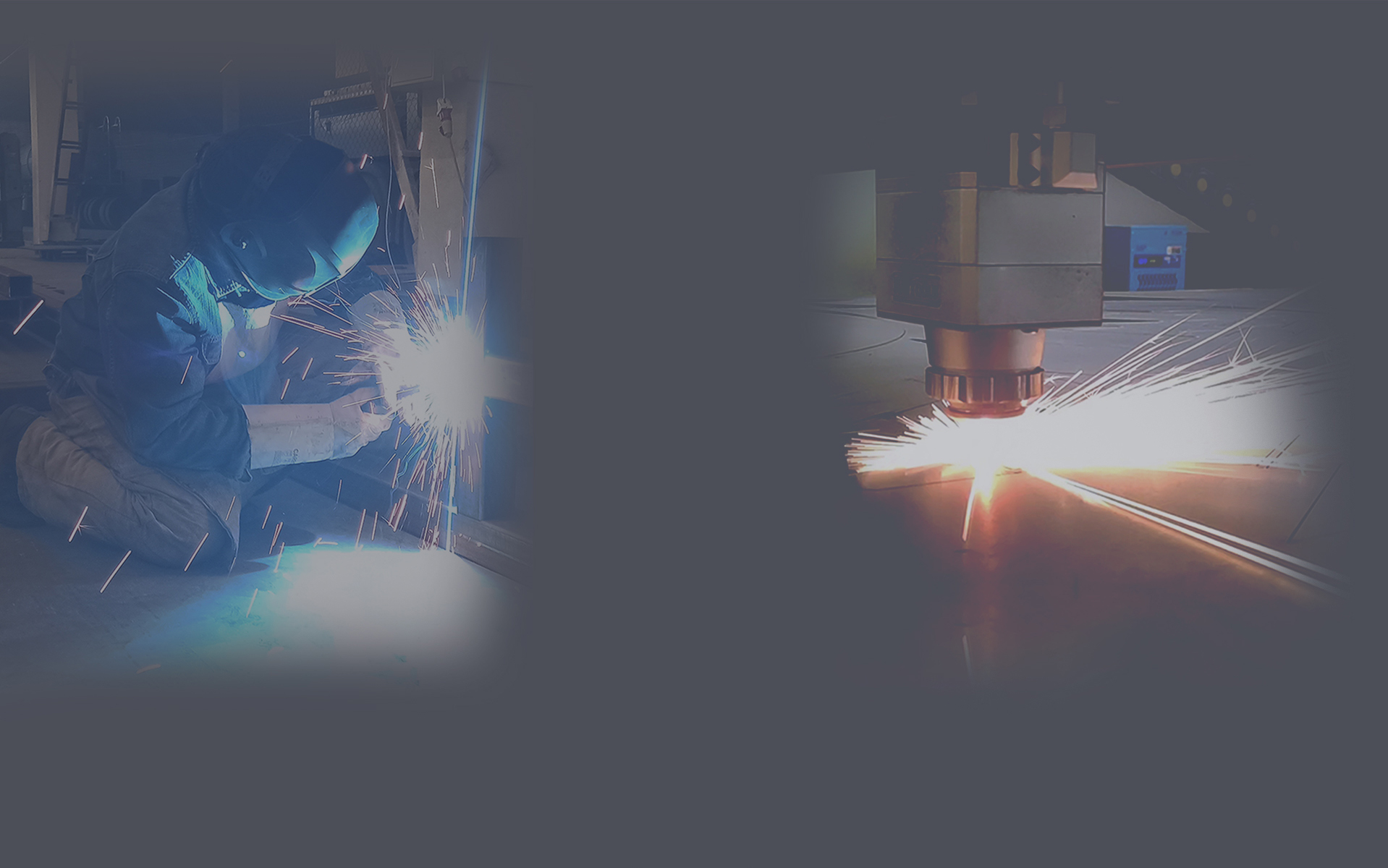
Weighing platform doser, with a screw feeder, is designed forpackaging by weightdosing of dust-forming (dusting) bulk products into finished containers or packaging (package, sack, box, jar, bottle). It operates in a semi-automatic mode and requires the operator to install the container, give a command to start dosing, and collect the filled container. The equipment is used for packaging and packaging starch, powdered sugar, chalk, flour, toner, etc., with a capacity of up to 1000 doses per hour.
Characteristic.
Power supply, V/Hz | 380/50 |
Power consumption, kW/hour | 2 |
Pneumatic supply**, atm./l.min. | none |
Length / Width / Height (max), mm | 1700/1200/2200 |
Weight (max), kg | 160 |
Productivity (max)*, packs/hour | 500-600 |
Storage bin volume, l | 100 |
Dosage range, g | 1000 – 5000 |
Package length/width (max), mm | 400/240 |
* Productivity depends on the dose weight and the properties of the dosing product.
Description of work.
The product being dosed is poured down the inclined walls of the hopper to a horizontal pipe located at the bottom. An auger passes through the pipe, one end of which is fixed in the electric drive. Pouring into the pipe, the product fills the cavities between the screw surface of the auger and the inner surface of the pipe.
Upon receiving a signal to start operation (the operator pressing a button or pedal), the Libra controller, located in the control unit, supplies power to the electric drive, which begins to rotate the auger.
While rotating, the auger moves the product being dosed (along its screw surface) from the hopper to the nozzle, through which the product is poured into the packaging (container) installed on the weighing table. The container filled with the product creates pressure on the weighing table, which is attached to the frame of the equipment using strain gauges (strain gauges).
The Libra controller monitors the packaging achievement of the set weight indicators (dose size) by the signal from the strain gauges, changing the auger operation modes: from the moment the dose is dispensed until the set threshold value, the auger rotates quickly (coarse dosing mode), and after reaching the threshold value, the auger speed decreases and the product is added (fine dosing mode).
The use of these two modes is necessary to ensure sufficiently high productivity while eliminating excess dose: the coarse dosing mode ensures rapid filling of the packaging, and the fine dosing mode eliminates accidental excess dose. The auger rotation speed in these modes is determined by the values set on the frequency converter.
When the set weight parameters (dose size) are reached, the controller stops the auger rotation and stops dispensing the product into the packaging. The operator must replace the filled packaging (container) with an empty one, after which he can again give a signal to start work (by pressing a button or pedal), continuing the dosing process.
Features.
The dispenser is optimal for dosing powdery dust-forming (dusting) products (flour, powdered sugar, starch, chalk, toner). The dispenser is capable of dosing other free-flowing products, including non-dust-forming ones, but the presence of a screw that moves the product in a closed space (pipe) directly to thepackaging and, as a result, reduces dust formation, leads to the fact that the dispenser is mainly used for dosing dust-forming bulk products. Not applicable for large fraction products, fragile and sticky products that can jam the auger or crumble during the dosing process.
The weighing doser allows you to arbitrarily change the portions of the product being packaged, as well as achieve fairly accurate dosing. Unlike volumetric dosers, it has no restrictions on changing the product being dosed. The vertical arrangement of the auger allows for higher quality and more accurate dosing of the product, and the presence of a stirrer reduces the likelihood of the product sticking to the walls of the storage bin.
This equipment is available in one model HD-20-B, with modifications in terms of weight parameters, dosage, and overall dimensions of the packaging.
SERVICE AND WARRANTY
We provide service.
We use original spare parts and consumables for sunflower harvesters.
Types of repair work:
– defect detection (detection of malfunctions) of the harvester;
– full or partial replacement of the bottom of the harvester Every broken INTAPACK harvester that we take in for repair is completely repaired in our own workshop. First, the harvesters are thoroughly cleaned and inspected for defects. Then the drive components and bearings are checked for their efficiency, the harvester is adjusted correctly and all worn parts are replaced. Finished products are painted.
We are sure that the performance of refurbished harvesters is not inferior to new harvesters. With the help of repair, you can restore the resource of harvesters up to 95%. INTAPACK service and repair specialists have the necessary qualifications. The cost and terms of repair work are determined in advance.
Original spare parts are always in stock: bushings, sprockets, chains, knives, oil seals, gears, washers, shafts, plates, rings, keys, knife nut covers, etc. In order to find out which part is necessary for a particular breakdown, as well as the cost of repair work, contact professionals. Contact us and we will provide professional advice.
Apie kompaniją
Apie kompaniją
Apie kompaniją – INTAPACK yra nauja inžinerijos įmonė.
Pagrindinė veiklos sritis – technologinės įrangos projektavimas ir gamyba individualioms užduotims įvairiems pramonės sektoriams.
Turime savo gamybos patalpas, kurios leidžia kontroliuoti visą procesą – nuo kūrimo iki gaminių gamybos ir pristatymo. Siekiame nuolatinio tobulėjimo ir naujovių, kad mūsų klientai visada gautų geriausią jų poreikius atitinkančią įrangą.
Mūsų specialistai turi didelę patirtį mechaninės inžinerijos srityje, kuri leidžia pasiūlyti individualius sprendimus kiekvienam klientui. Taip pat teikiame įrangos montavimo, priežiūros ir remonto paslaugas, suteikdami pilną pagalbos ciklą visuose eksploatacijos etapuose.
contacts
Address of production facilities
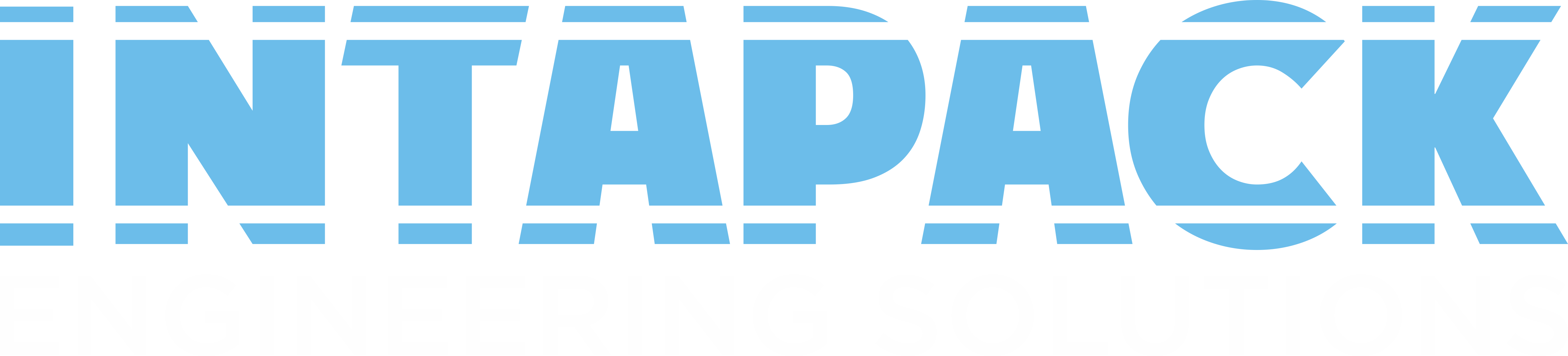
Ukraine Cherkasy region, Cherkasy city
Khimikov avenue 74 D
Khimikov avenue 74 D
тел. +380689027878