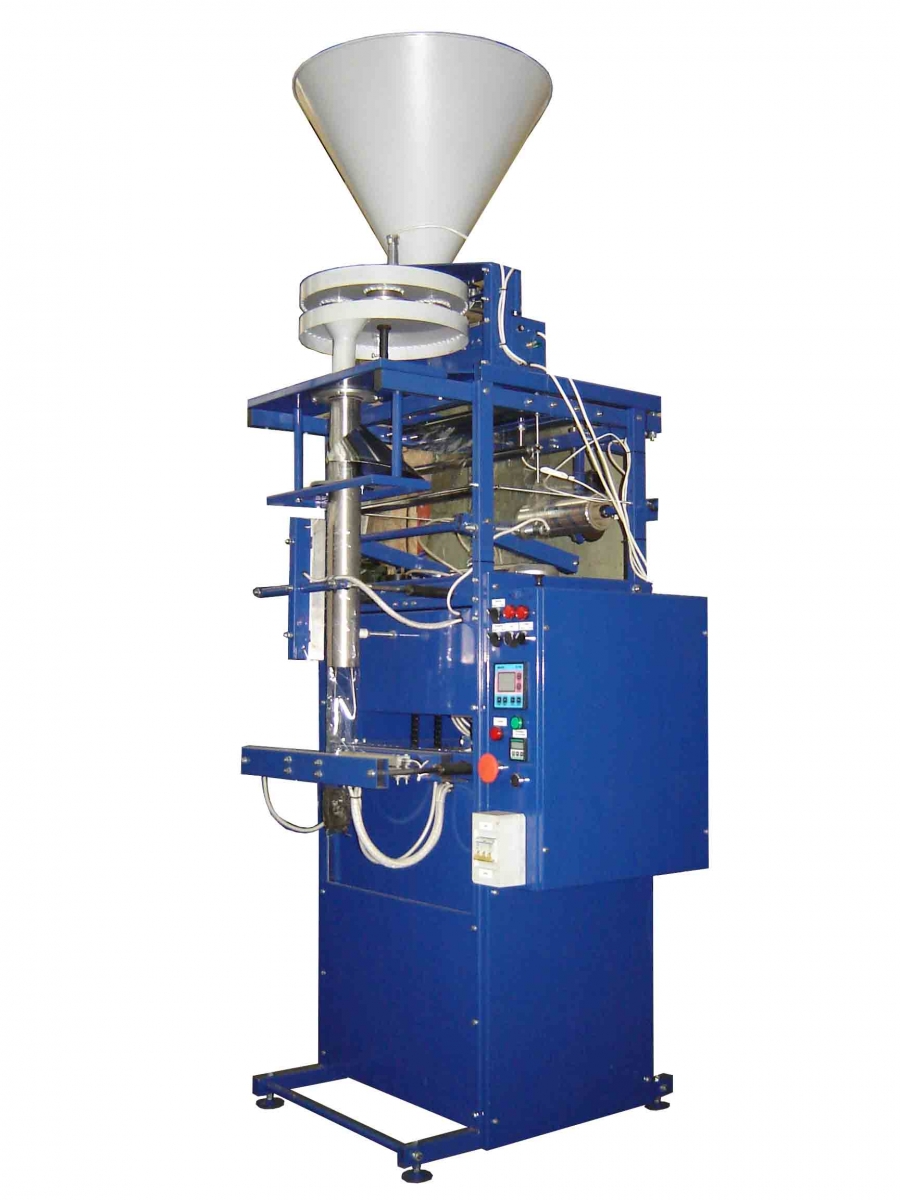
The filling and packaging machine provides a continuous cycle of volumetric dosing of free-flowing products (cereals, nuts, coffee) and packing them in a pillow bag (stand-up bag) made of polymer films (polypropylene, duplex, triplex, laminated paper, nylon, filter paper). The packaging process requires virtually no human intervention and is fully automated.
The equipment consists of a pneumatic packaging machine and a volumetric cup dispenser.
The filling machine is the most productive among the models of the “Pneumo” series, has the lowest price (among similar equipment models), and has the ability to change the size and characteristics of packaging materials.
Characteristics.
Power supply V/Hz | 380/50 |
Electricity consumption kW/hour | 1,5 |
Pneumatic supply, atm./l.min. | 6/250 |
Length/Width/Height (not more than), mm | 1100/1200/2300 |
Weight (not more than), kg | 280 |
Film roll width/diameter (not more than), mm | 380/300 |
Productivity*, packs/hour. | 2100 |
Volume of storage bin, l | 60 |
Dosage limits, cm3 | 50-1000 |
Length/Width of package (max.), mm | 300/180 |
* The equipment performance depends on the dose volume, the properties of the packaging material, the length of the package, as well as the operator’s efforts.
** To ensure the operation of the pneumatic drives of this packaging machine, a “compressor” is required (supplied separately).
Description of work.
The packaged product is poured through the hopper neck into a “cup” secured to the carousel and located under the neck. The carousel has such an arrangement of “cups” that when one “cup” is under the neck, the opposite “cup” is above the tube of the sleeve-forming device. That is, the “cup” located under the hopper neck is filled with product and the “cup” located above the tube is emptied at the same time.
When receiving an impulse from the microcontroller of the control unit of the packaging machine, the electric drive of the dispenser rotates the carousel, shifting the filled “cup” from the hopper neck towards the tube and placing the next empty “cup” under the neck. Upon reaching the tube, the filled “cup” empties, pouring its contents into the tube, on which the packaging film with a sealed back seam and bottom (package blank) is rolled into a tube (sleeve). Spilling through the tube, the product fills the package.
After dispensing a dose of the product, the microcontroller, using pneumatic drives, activates the soldering unit. The soldering unit of the filling machine uses the principle of constant heating and, in one step, simultaneously seals the top seam of the filled package, the bottom and side seams of the next package with a “euro-roller” type of seam.
At the same time, at the moment of welding, the horizontal jaws of the sealing unit (carriage) are shifted downwards by the set length of the package. Since the jaws move downwards without unclenching, they pull the packaging film along with them. The roll is unwound and the film is rolled up, through the collar, into the sleeve around the tube.
When the carriage reaches the bottom point, the filled package is separated by cutting the film with a mechanical toothed knife. At the same time, the microcontroller sends a pulse to the electric drive of the dispenser to rotate the drum and pour the contents of the “cup” into a new package, opens the horizontal jaws and moves them upward to seal the next package. The cut package falls on the floor, into a special container (box) or onto a discharge conveyor.
Additionally, the microcontroller monitors the moments of emptying the dispenser hopper, the end of the roll of packaging material and other emergency situations.
Peculiarities.
The packaging machine is ideal for packaging products that have good flowability and are capable of uniformly and quickly filling free cavities, such as cereals, rice, seeds, grain, seeds, salt, sugar, tea, coffee beans. The model is not suitable for packaging dusty or hard-to-flow products (flour, raisins, corn sticks). It is also necessary to take into account that due to the use of a volumetric dispenser, this packaging equipment is not universal and has restrictions on the change of the packaged product.
The packaging machine requires floor placement and has restrictions on the width of the packaging film used and the height of the formed package, specified in the technical specifications. It is possible to manufacture a packaging machine of increased dimensions – the maximum film width will be up to 500 mm, and the package height up to 400 mm.
Equipment.
Standard equipment:
Volumetric cup dispenser with a storage bin;
Former of 3-seam packaging “pillow” – collar (up to 380 mm);
System of automatic carriage feeding of packaging material along the length and along the “photo mark”;
Unit for sealing longitudinal and transverse seams of the packaging with the “euro-roller” type;
Unit for putting the date on the seam of the packaging (day, month, year “XX XX XX”);
Electronic control unit with light indication and monitoring of emergency situations.
Additional equipment:
Tube with collar (for changing the film width);
Unit for forming a “stand-up package”;
Thermal printer (from 6 characters, at any point of the package);
Device for applying a punch to the seam (“Euro loop”, “Euro punch”);
Protective cover;
Compressor.
Equipment:
Electric drives – STM (Italy);
Pneumatic drives – CAMOZZI (Italy);
Used – Libra, MiKra (Ukraine);
Frequency converters – INVT, HYUNDAI (Korea);
Product contact units – 304 steel.
Possibilities: 2100 packs/hour.
Type of packaging: package (pillow/standing).
Products: dust-forming products.