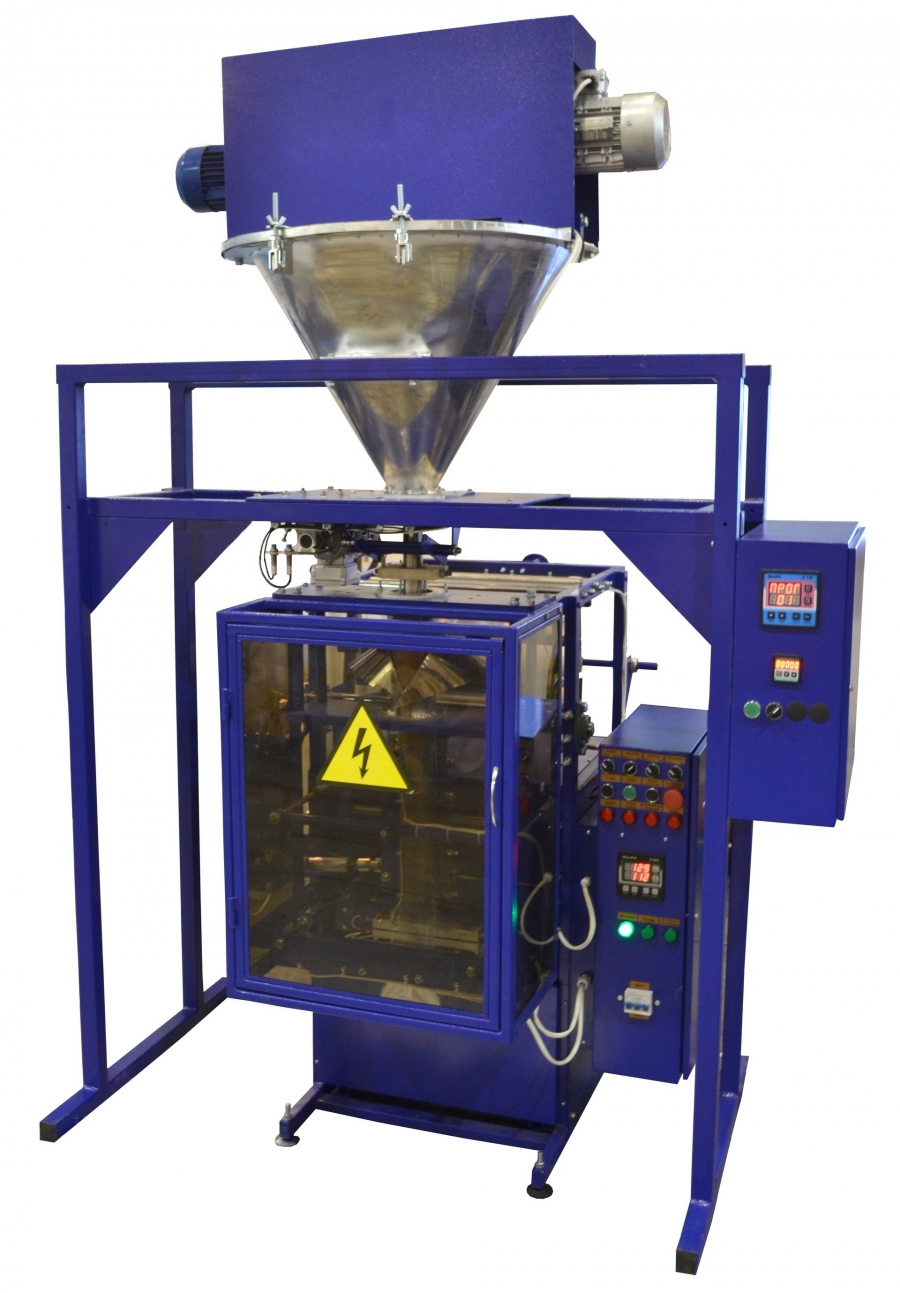
The filling and packaging machine, model AF-45-H, is designed to provide a continuous cycle of filling, volumetric method, and packaging of dust-forming products (flour, dry milk, starch, cement, chalk) in polymer soft packages (pillow, stand-up bag)
This equipment consists of a mechanical packaging machine and a volumetric screw dispenser.
The filling and packaging machine with a screw dispenser is the most compact and easy to maintain equipment (among similar models), does not require a compressor, and also has the ability to change the size and characteristics of packaging materials.
Characteristics.
Power supply, V/Hz | 380/50 |
Electricity consumption, kW/hour | 2,5 |
Length/Width/Height (not more than), mm | 1700/1200/3100 |
Weight (not more than), kg | 460 |
Film roll width/diameter (max), mm | 380/300 |
Productivity (max.)*, packs/hour | 1800 |
Volume of storage bin, l | 60 |
Dosage range, cm3 | 50 – 1000 |
L/W of package (max), mm | 300/180 |
* Productivity depends on the volume and properties of the dose, the length of the package, and the properties of the packaging material.
Description of work.
The packaged product is poured down the inclined walls to the hopper neck, connected to the tube of the sleeve-forming device. A vertically positioned auger passes through the neck and the tube, the upper part of which is fixed in the electric drive. Spilling through the neck, the product fills the cavities between the screw surface of the auger and the inner surface of the tube. To prevent it from spilling, a valve is provided in the lower part of the tube.
When power is supplied from the CT201 meter, located in the control unit of the packaging machine, the electric drive begins to rotate the auger, thereby moving the product from the hopper down the tube. The rotation speed of the auger is determined by the values set on the frequency converter. In addition, the electric drive activates the “stirrers” in the hopper, which mix the product, preventing bridging and better pouring of the product to the hopper neck.
During the rotation of the screw, the valve in the lower part of the tube opens, and the product moved by the screw is poured into the packaging film rolled up on the tube like a sleeve with a sealed back seam and bottom (packaging blank). After reaching the number of pulses set on the counter “CT201”, the power supply to the electric drive is stopped, the screw stops and the valve on the tube closes, cutting off the delivery of a dose of product to the packaging blank. At the same time, the counter “CT201” sends a pulse to the microcontroller that controls the operation of the packaging machine.
Having received the pulse, the microcontroller activates the packaging film pulling mechanism. When pulling, the roll unwinds and the film is rolled up, through the collar, into the sleeve around the tube. Having pulled the film to the required distance (determined by the photo mark or the value of the parameter “СЧt. 1”), the microcontroller activates the soldering unit.
The soldering unit uses the principle of constant heating and simultaneously seals the top seam of the filled package, the bottom and side seams of the next package with the “Euroche” type of seam in one go. At the same time, at the moment of welding, the filled package is separated by cutting the film with a mechanical serrated knife. The cut package falls on the floor, into a special container (box) or onto a discharge conveyor.
At the same time, the microcontroller of the packaging machine sends a pulse to the counter “CT201”, which supplies power to the electric drive of the dispenser, filling the next package.
Additionally, the microcontroller monitors the moments of emptying the hopper, the end of the roll of packaging material and other emergency situations.
Peculiarities.
The filling and packaging machine is optimal for packing dust-forming bulk products such as flour, dry milk, starch, cement, chalk. The machine allows arbitrary change of the dose size and the packed product, but it should be borne in mind that this packaging machine uses the volumetric dosing method, measuring the dosed product not by weight, but by the number of revolutions of the auger. Therefore, when changing the dosed product, it is necessary to take into account its density, since with the same number of revolutions for different products, the weight of the portions may differ.
The difference between this machine and a similar AF-35-H is the use of a mechanical packaging machine, which does not have pneumatic drives. This, accordingly, does not require the use of a compressor, which means the machine is quieter in operation. In addition, this machine has smaller dimensions than the AF-35-H.
The filling and packaging machine has significant dimensions and weight and requires floor placement. There are also restrictions on the width of the film used and the height of the packaging formed, indicated in the technical specifications.
Equipment.
Standart equipment:
Volumetric screw dispenser with a storage bin with agitator;
Former of 3-seam packaging “pillow” – collar (up to 380 mm);
Automatic belt feed system for packaging material by “photo mark”;
Sealing unit of the “euro-roll” type of longitudinal and transverse seams of the packaging;
Unit for putting the date on the seam of the packaging (day, month, year “XX XX XX”);
Electronic control unit with light indication and monitoring of emergency situations.
Additional equipment:
Tube with collar (for changing the film width);
Unit for forming a “stand-up package”;
Encoder (for pulling the film along the length of the package);
Thermal printer (from 6 characters, at any point of the package);
Device for applying a punch to the seam (“Euro loop”, “Euro punch”);
Protective cover.
Equipment:
Electric drives – STM (Italy);
Used – Libra, MiKra (Ukraine);
Frequency converters – INVT, HYUNDAI (Korea);
Product contact units – 304 steel.
Possibilities: 1800 packs/hour.
Type of packaging: package (pillow/standing).
Products: dust-forming products.