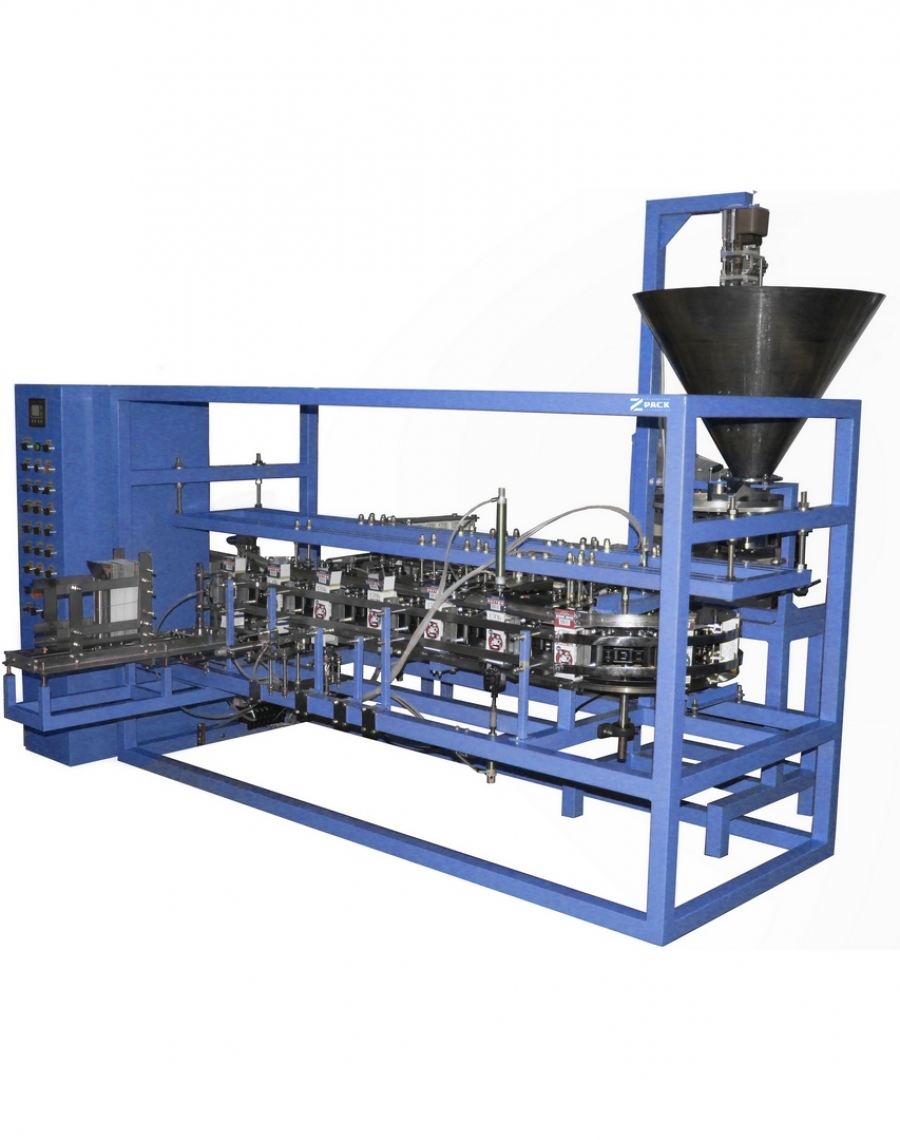
Packaged products: Nuts, Cinnamon, Chips, Candies, Dragee, Corn sticks, Cookies, Gingerbread, Dumplings, Washing powder, Dry pet food, Cereals, Salt, Soda, Cocoa powder, Coffee beans, Ground coffee, Sublimated coffee, Pasta, Starch, Seeds, Beans, Peas.
Equipment.
In accordance with your request, we offer to manufacture the following equipment:
– Paper bag packing line, which includes:
– frame;
– control panel;
– receiving magazine for empty bags;
– unit for removing a bag from the magazine, straightening and installing an empty bag in the receiving tray of the conveyor;
– screw dispenser (for packing flour and other dusty products).
– step conveyor with receiving cells for bags;
– bag top folding unit;
– unit for cutting off excess part of the bag top;
– unit for wrapping and sealing the bag top;
– unit for removing the bag onto the tray;
– unit for putting the date on the bag.
Purpose and scope of application.
Line for packing various bulk products into paper bags.
If equipped with a screw dispenser, the line can pack flour, starch, soda and other dusty products into 1, 2 or 3 kg bags (packing into 5 kg bags is not provided).
General principle of operation.
Finished paper bags are taken out of the magazine (there are more than 200 of them), automatically opened and placed in a cell of the conveyor, which provides step-by-step movement. The bag, being in the cell, is filled with the product, then after the product is pressed, the bag gets to the folding unit of the upper part. At the next position, the excess part of the top of the bag is cut off, then the bag is wrapped and sealed. The finished filled and sealed bag goes to the accumulation tray, from where it is conveniently fed to the table of the thermal tunnel for group packaging.
Line composition.
The line is a metal frame (pos. 16), on which the following units are mounted:
– Step chain conveyor with receiving cells for bags (pos. 1). Carrying out step-by-step movement of bags between positions.
– Empty bag magazine and bag extraction unit from the magazine (pos. 3). Carries out individual bag removal from the blank magazine and bag feeding by the manipulator to the bag bottom opening unit.
– Bottom opening unit (pos. 4). Carries out bag bottom opening, straightening and installing the bag in the receiving cell of the conveyor.
– Bag top opening unit (pos. 5). Opens the bag under the dispenser with the help of vacuum suction cups, and then fixes the top of the bag with curtains.
– Screw dispenser (pos. 19). Provides flour dosing and filling of the bag.
– Shrinkage unit (pos. 6). The bag is vibrated by means of a pneumatic drive, which helps to reduce the volume of the packaged product in the bag.
– Empty bag ejection unit (pos. 6). Removes the empty bag from the receiving cell, preventing its further movement to the area of folding the upper seam and sealing the bag.
– Bag top folding unit (pos. 7). Tramps the top and forms the upper edge of the bag for subsequent folding.
– Cutting unit (pos. 8). Aligns the upper edge and cuts off the excess part of the bag, leaving only the edge necessary for turning up.
– First bend unit (pos. 8). Turns the upper edge of the bag by 180°.
– Second bend unit (pos. 8). Presses the bend line and folds the upper flap in the horizontal direction.
– Cold glue application unit (pos. 9). Doses a portion of glue and applies it to the bag after the second fold unit.
– Bag top pressing unit (pos. 8, 11). Presses the bag flap with glue applied to it for high-quality gluing.
– Finished bag unloading unit (pos. 2). Removes the bag from the conveyor cell and pushes it onto the finished product tray.
– Date stamping unit (pos. 12). Puts the packing date on finished bags (up to 6 characters in two lines) when they are on the finished product tray.
*Flour is fed into the hopper of the auger doser either by a screw feeder or by a screw loader:
– Screw feeder. Provides flour supply to the screw doser hopper from the Customer’s silos.
– Screw loader.
Provides flour supply to the screw doser hopper from the receiving hopper.
Technical specifications.
Productivity, packs/min |
до 14 – 18 |
Dosage range, kg | 1 – 3 |
Installed capacity, kW, no more than | 3 |
Supply voltage, V | 380 |
Compressed air pressure MPa | 0,6 |
Compressed air consumption, l/min no more than | 500 |
Temperature of production premises, оС | ≥15 |
Overall dimensions L*W*H, mm | 3600*2500*2500 |
Weight, kg (not more) | 1000 |
Characteristics.
Characteristic | Value |
---|---|
Productivity, packs/min | up to 20 |
Box dimensions, mm | up to 180x100x300 |
Power supply parameters | 220V, 50Hz |
Installed capacity, kW | 1,5 |
Dimensions, mm, no more than | 2700х2300х1400 |
Weight, kg, not more than | 480 |
Description of work.
The line ensures the extraction of the box blank from the magazine, folding and sealing the bottom of the pack, filling with the packaged product, folding and sealing the top of the box, and also putting the date. After this, the filled and sealed boxes are extracted from the conveyor cells and go to the accumulator.
Peculiarities.
Compressor is not included.
Equipment warranty: 12 months for commissioning; 6 months in other cases.
Equipment.
Depending on the type of product being packaged, the line can be equipped with a weighing, auger or volumetric dispenser.
Possibilities: up to 20 packs/min.
Type of packaging: cardboard boxes.
Products: bulk products.