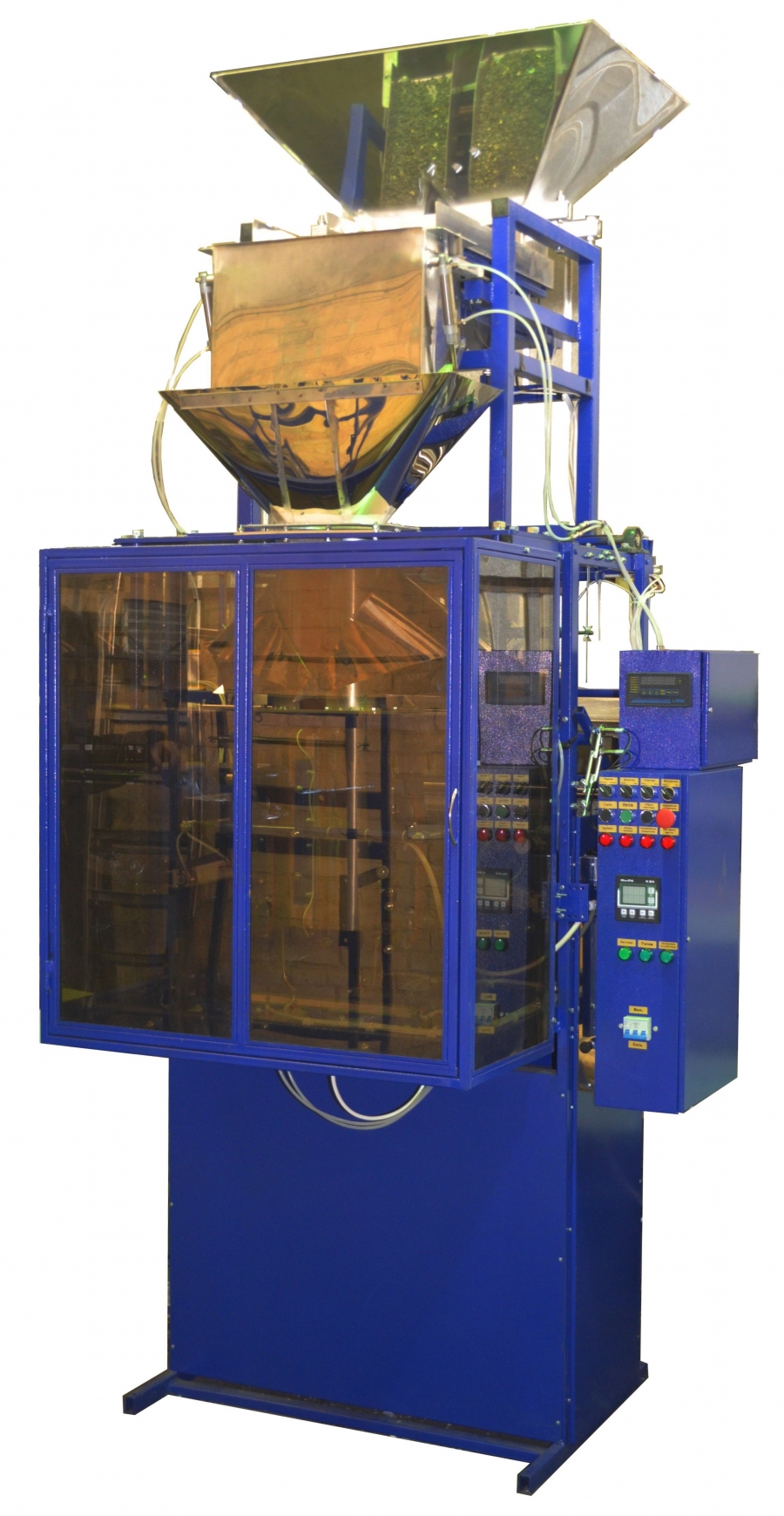
This filling and packaging machine is designed to provide a continuous packaging cycle, weighing the dosing of bulk products (washing powder, bird feed, seeds, corn sticks) and packing them in polymer single-layer or multilayer films (polypropylene, duplex, triplex).
The equipment consists of a vertical packaging machine and an electronic weighing batcher with a belt or vibration feeder.
The equipment allows for dosing (packaging) of bulk products by weight from 0.5 to 10 kg, with minimal error, and packing of bulk products in large packages (bags, sacks).
Characteristics.
Power supply, V/Hz | 380/50 |
Electricity consumption, kW/hour | 3,5 |
Pneumatic supply**, atm./l.min. | 6/400 |
Length/Width/Height (not more than), mm | 1300/1500/3800 |
Weight (not more than), kg | 800 |
Film roll width/diameter (max), mm | 850/400 |
Productivity (max.)*, packs/hour | 600 |
L/W of package (max), mm | 500/400 |
Dosage range, g | 500 – 10 000 |
Volume of storage bin, l | 100 |
* Productivity depends on the weight of the dose, the length of the package, and the properties of the packaging material.
** To ensure the operation of the pneumatic drives of this packaging machine, a “compressor” is required (supplied separately).
Description of work.
The packaged product is poured through the hopper neck onto the feeder*, with the help of which it is fed into the weighing bucket. The bucket is attached to the frame of the weigh batcher on a strain gauge (strain gauge). When the specified weight parameters are reached, the strain gauge sends a signal to the batcher control unit (the Libra controller), which stops the vibrating tray, stopping the product feed.
* The feeder can be made in the form of a vibrating tray or a polyurethane conveyor belt (the belt is more suitable for fragile, hard-to-flow products; in other cases, a vibrating tray is used). The feeder is controlled by the control unit, which, by supplying power to an electric motor or an electromagnet, makes the conveyor belt rotate or creates vibrations in the vibrating tray, thereby moving the product from the hopper neck to the tube funnel.
Upon receiving a pulse from the control unit of the packaging machine (the “Unloading” signal), the doser controller sends a signal to open the weighing bucket*. The bucket opens, pouring its contents into the funnel. Through the funnel, through the tube of the sleeve-forming device, the product is poured into a folded tube (sleeve) of packaging film with a sealed back seam and bottom (packaging blank). At this time, the controller turns on the feeder to fill the weighing bucket with the next portion of the product.
The seam of the bottom of the package is clamped in the horizontal heating elements of the sealing unit, which remain compressed until the end of the dose dispensing. This eliminates the pressure of the dose on the seam and the possibility of its rupture as a result of an impact when the dose falls.
The operation of the packaging machine is controlled by a microcontroller located in the control unit, which, after unloading the weighing bucket (dispensing a dose of product), releases the heating elements of the sealing unit and turns on the feeding of the packaging material. The pulling is performed using an electric motor and belts to the length set by the operator (determined by the photo mark or the value of the parameter “СЧt. 1”). When pulling, the roll is unwound and the film is rolled up through the collar into the sleeve around the tube.
Having pulled the film to the required distance, the control unit activates the sealing unit: it compresses the heating elements, fixing the packaging material and presses the vertical welding element to the tube, starting the process of welding the packaging seams.
The sealing unit of the packaging machine uses the principle of constant heating and in one step simultaneously seals the top seam of the filled package, the bottom and side seams of the next package with the “euro-roll” type of seam. At the same time, at the moment of welding, the filled package is separated by cutting the film with a mechanical serrated knife. The cut package falls on the floor, into a special container (box) or onto a discharge conveyor.
Peculiarities.
This packaging machine is ideal for packaging products that are convenient to sell in large packages (bags, sacks). Such products can be: washing powder, bird feed, seeds, corn sticks, animal fillers, sugar.
The machine is not suitable for packaging highly dusty products. It should be taken into account that due to the use of a weigh batcher, this model of the packaging machine is universal and has no restrictions on changing the product being packaged.
It should be taken into account that the soldering unit of this packaging machine does not allow the use of polyethylene (PE) films for its work.
The packaging machine requires floor placement and has restrictions on the width of the packaging film used and the height of the formed package, specified in the technical specifications.
Equipment.
Standart equipment:
Electronic weighing batcher with belt or vibration feeder and storage bin;
3-seam “pillow” – collar packaging former (up to 850 mm);
Automatic belt feed system for packaging material using “photo mark”;
Euro-stitch sealing unit for longitudinal and transverse packaging seams;
Date stamping unit on packaging seam (day, month, year “XX XX XX”);
Electronic control unit with light indication and emergency situation monitoring.
Additional equipment:
Loading and discharging conveyor;
Tube with collar (for changing the film width);
Unit for forming a “stand-up package”;
Encoder (for pulling the film along the length of the package);
Thermal printer (from 6 characters, at any point of the package);
Unit for forming a handle on the package (“3 fingers” or “Euro-cut”);
Unit for forced air blowing (cooling) of the seams of the package;
Protective cover;
Compressor.
Equipment:
Electric drives – STM (Italy);
Pneumatic drives – CAMOZZI (Italy);
Used – Libra, MiKra (Ukraine);
Frequency converters – INVT, HYUNDAI (Korea);
Product contact units – 304 steel.
Possibilities: 600 packs/hour.
Type of packaging: bag (pillow/standing).
Products: bulk products.