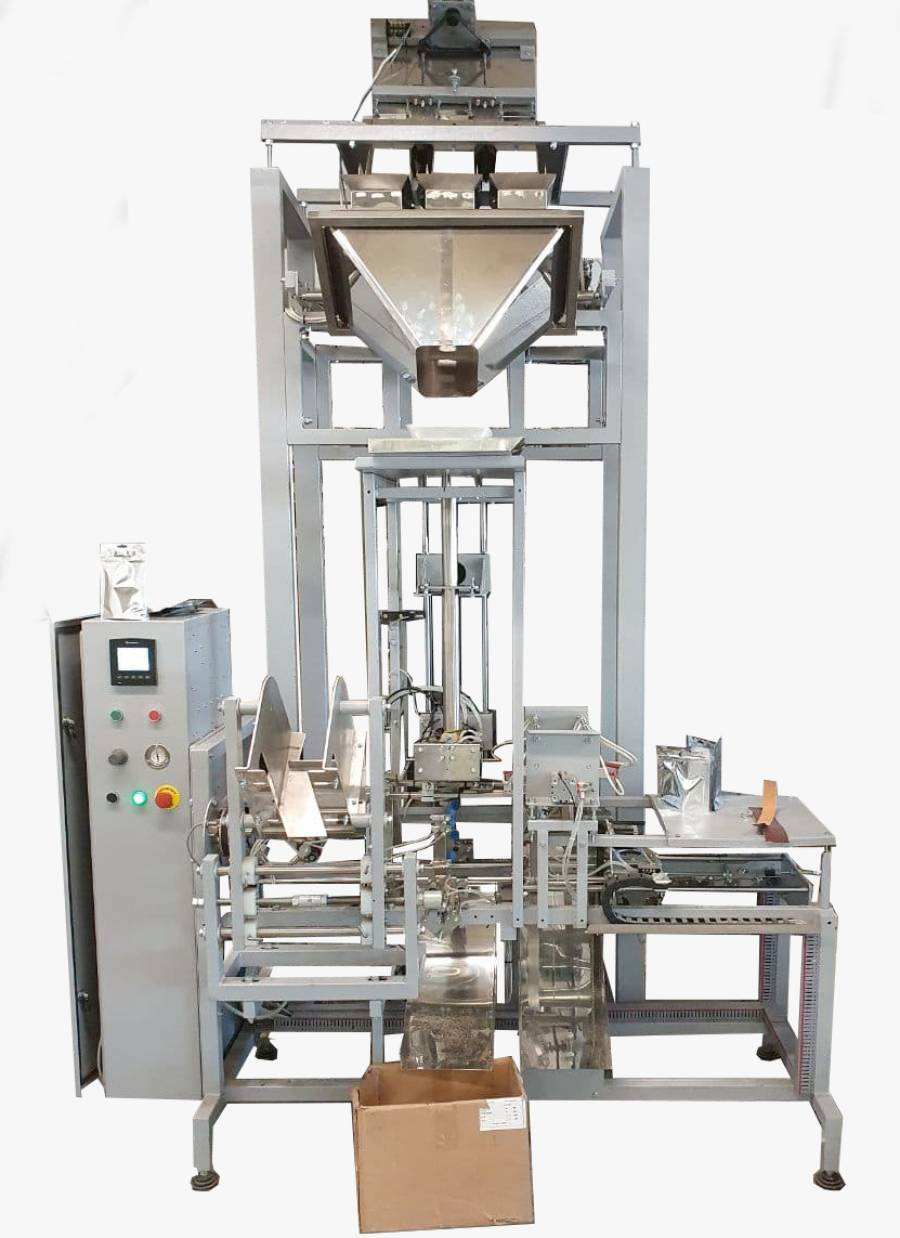
The horizontal filling and packaging machine AF-35-D is designed to create a continuous cycle of packaging bags in the form of “doy-pack”, pre-dosed food and non-food free-flowing, liquid and paste-like products (cereals, sugar, coffee, tea, grains, nuts, mayonnaise, ketchup, etc.).
The horizontal packaging machine is a universal device that allows you to work as an independent complex for packaging products, and as part of filling and packaging lines using volumetric or weigh batchers.
Characteristics.
Power supply, V/Hz | 220/50 |
Installed capacity, kW | 1 |
Pneumatic supply, atm./l.m. | 6/400 |
H/W/D (not more than), mm | 2500/1700/2300 |
Weight (not more than), kg | 450 |
Thickness of packaging material, µm | 60-150 |
Packaging material | multilayer films |
Package dimensions H/W, mm | height – 180…280, width – 140…240 |
Permissible dosage limits, g | 50-1500 |
Productivity (kinetic), packs/hour | 1200 |
Type of sealing of packaging seams | constant heating |
Capacity of the bag store, pcs. | 250…300 |
Monitoring emergency situations | yes |
Possibility of working with a ZIP lock | yes |
Description of work.
The operator places a stack of packages in the accumulator, from where, using a rotary mechanism with vacuum suction cups, the package is pulled out and moved to the working area.
After the package is brought out to the working area, and one cycle has been processed by all units of the machine, the crossbar of the package movement mechanism moves all the packages in the working area of the machine to the next processing stage.
The package moved to the top opening position is gripped on both sides by suction cups and stretched. The unsealed top of the package opens, and if the ZIP lock is closed, it is bent back. The grips of the ZIP opening mechanism enter and close between the bent edges of the top. Having clamped the edges of the package, the grips move apart in opposite directions, opening the ZIP lock, after which the grips open and rise upward.
A cone is lowered into the package with the open top moved to the position. Having reached the bottom of the bag, petals come out of the cone and open the bottom, giving the bag a three-dimensional shape, after which the cone moves to the upper position.
After the bag is opened with the help of the vertical box, the box, descending, enters with closed flaps into the upper part of the fully opened bag, moved to the filling position. The flaps open, and the dose of the product from the weigh batcher through the receiving funnel and the box gets into the bag, after which the box moves to the upper position.
The next unit stretches the top of the bag with special spring-loaded fingers, thereby preparing it for the last operation – sealing the top.
When the carriages close, the welding pads clamp the filled bag moved to the position, with a stretched top, and weld the upper seam of the bag. Simultaneously with the welding of the upper seam of the bag, the rubberized strips close and close the ZIP-lock.
The bag moved to the position of the upper seam welding unit, filled and with the top stretched, is clamped by the welding pads and the upper seam of the bag is welded. Simultaneously with the welding of the upper seam of the bag, the rubberized strips are closed and the ZIP-lock is closed.
After the upper seam welding unit is opened, the bag falls into the chute and is carried away along it to the box or to the discharge conveyor.
In the automatic mode of the machine, all commands to the drives are sent by the controller. The machine stops in case of empty bags, product in the hopper or an emergency. Information about the reason for the stop is displayed on the operator control panel of the machine.
Peculiarities.
The doy-pack filling machine of the AF-35-DV series is used for the automatic process of filling almost any type of free-flowing products (coffee, tea, spices, salt, sugar, cereals, etc.) into ready-made doy-pack bags.
Due to the use of a linear weighing batcher, this device allows for the filling (dividing into doses) of products into ready-made bags with maximum accuracy. The weighing batcher of this line has a memory for 15 programs, which simplifies the operator’s work from frequent readjustments to different products. The packaging unit of this machine allows the use of doy-pack packages of various sizes specified in the technical specifications. It is possible to manufacture equipment with individual parameters.
The filling complex is available in the AF-35-DV model with modifications of the weighing batcher (1, 2, 3, 4 streams). Model AF-35-DV1 has 1 stream of the weighing batcher with a capacity of up to 300 packs/hour. Model AF-35-DV4 has 4 weighing batcher streams with a capacity of up to 1200 packs/hour. The packer also has the ability to connect other types of batchers (weighing combination multi-head, volumetric auger, volumetric liquid, volumetric carousel or belt).
Possibilities: up to 600 packs/hour.
Type of packaging: doy-pack bag.
Products: bulk, liquid products.