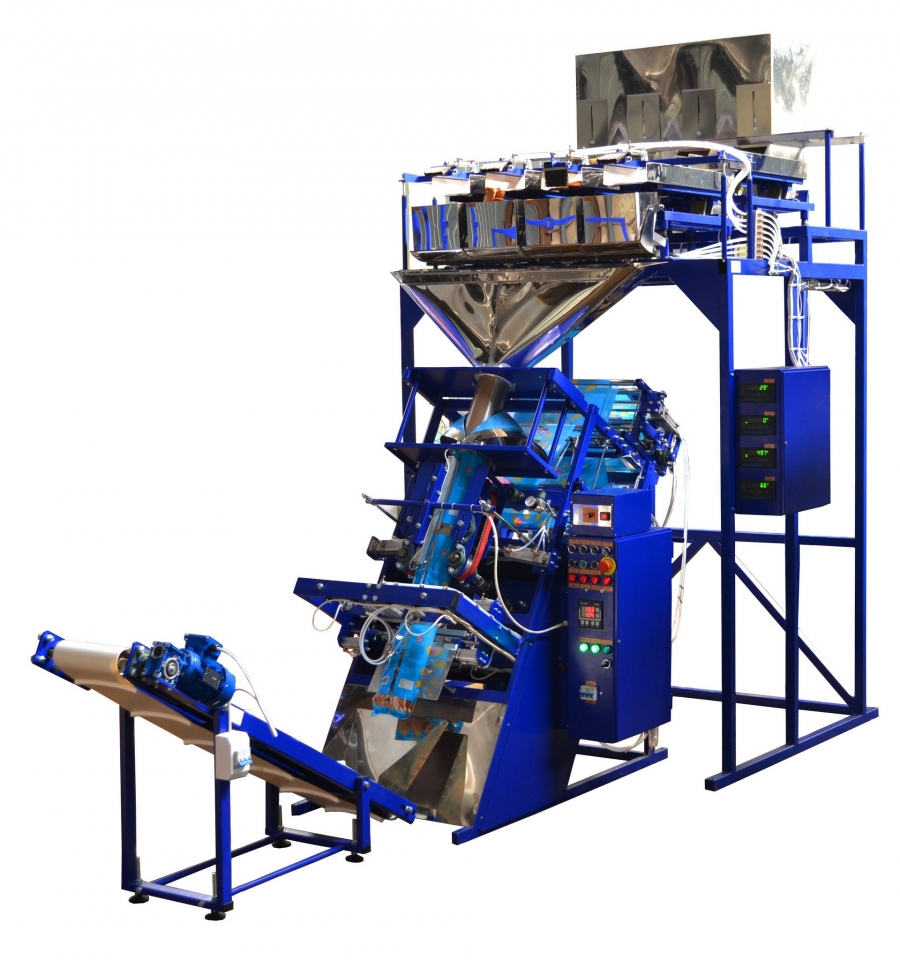
This filling and packaging machine is designed for the automatic process of filling (by weight) fragile bulk and hard-to-flow products (chips, cookies, sweets) and packing them in polymer soft packages, in the form of a pillow (stand-up bag).
The equipment consists of a packaging mnemonic automatic machine and a weighing electronic batcher.
The filling and packaging inclined unit, model AF-50-N-V, is universal, capable of effectively pulling various packaging films, with a width from 130 to 500 mm, as well as packing products with maximum accuracy.
Characteristics.
Power supply, V/Hz | 380/50 |
Electricity consumption, kW/hour | 2-2,4 |
Pneumatic supply**, atm./l.min. | 6/150 |
Length/Width/Height (not more than), mm | 1700/1200/2600-3100 |
Weight (not more than), kg | 440 |
Film roll width/diameter (max), mm | 500/300 |
Productivity (max.)*, packs/hour | 600-2700 |
Volume of storage bin, l | 60-240 |
Dosage range, g | 20–2000 |
L/W of package (max), mm | 400/240 |
* Performance depends on the weight and properties of the product being dosed, the length of the package and the properties of the packaging material.
** To ensure the operation of the pneumatic drives of this packaging machine, a “compressor” (supplied separately) is required.
Description of work.
The packaged product is poured through the hopper neck onto a vibrating tray, which vibrates with a given amplitude and feeds it into the weighing bucket. The bucket is attached to the dispenser frame using a strain gauge (strain gauge). When the specified weight parameters are reached, the strain gauge sends a signal to the dispenser control unit (the Libra controller), which stops the vibrating tray, ceasing the product feed.
When receiving a pulse from the packaging machine control unit (the Unloading signal), the dispenser controller sends a signal to open the weighing bucket. The bucket opens, pouring its contents into the funnel. Through the funnel, through the tube of the sleeve-forming device, the product is poured into a folded tube (sleeve) of packaging film with a sealed back seam and bottom (packaging blank). At this time, the controller turns on the vibrating tray to fill the weighing bucket with the next portion of the product.
The operation of the packaging machine is controlled by a microcontroller located in the control unit, which, after unloading the weighing bucket (dispensing a dose of product), activates the film pulling mechanism. When pulling, the roll is unwound and the film is rolled up through the collar into a sleeve around the tube. Having pulled the film to the required distance (determined by a photo mark or a specified value), the microcontroller activates the soldering unit.
The soldering unit uses the principle of constant heating and, in one step, simultaneously seals the top seam of the filled package, the bottom and side seams of the next package with a “euro-roll” type of seam. At the same time, at the moment of welding, the filled package is separated by cutting the film with a mechanical serrated knife. The cut package falls on the floor, into a special container (box) or onto the outfeed conveyor.
After opening the welded elements, the microcontroller of the packaging machine again sends an impulse to the “Libra” controller (the “Unloading” signal), filling the next package. Additionally, the microcontroller monitors the end of the roll of packaging material and other emergency situations.
Peculiarities.
The packaging machine is optimal for packaging products of any flowability, with the exception of highly dusty ones (flour, powdered sugar). Taking into account the dosing method and the characteristics of the weigh batcher, the packaging equipment allows you to arbitrarily change the portions of the packaged product, as well as achieve the most accurate dosage. It has no restrictions on changing the packaged product, which are present in machines with a volumetric batcher (AF-35-Ob, AF-45-Ob and AF-50-Ob).
The difference between this packaging equipment and similar AF-35-V and AF-45-V is the use of a pneumatic-mechanical packaging machine, which uses combined drives (the film is pulled by an electric motor and belts, and the compression and unclenching of the welded elements of the soldering unit is done with pneumatic drives). This combination significantly increases the speed of the machine and allows you to use wider packaging films than on the AF-45-V. At the same time, the presence of pneumatic drives requires the use of a compressor, and as a result increases the noise level of the filling machine, but the noise level does not reach that produced by the AF-35-V.
The machine requires floor placement and has limitations on the width of the film used and the height of the formed package, specified in the technical specifications.
The filling machine is available in models AF-50-V1, AF-50-V2, AF-50-V3, AF-50-V4. They differ from each other in the number of weighing buckets (“streams”): in AF-50-V1 1 “stream”, with a capacity of up to 600 packages/hour, and in AF-50-V4, respectively, 4 “streams”, with a capacity of up to 2700 packages/hour.
A separate modification of the filling machine is the use of a two-level weigh batcher, which allows more accurate and efficient dosing of hard-to-flow products that do not have constant flowability. For example, chips can either get stuck in the hopper neck (vibrating trays) or spill out in large, clumped portions. Accordingly, the dose size may have undesirable deviations from the specified one. To eliminate this, the dispenser uses 2 levels of vibrating trays.
Equipment.
Standart equipment:
Electronic weighing 1-4 flow dispenser with a storage bin;
Former of 3-seam packaging “pillow” – collar (up to 500 mm);
Automatic belt feed system for packaging material by “photo mark”;
Sealing unit of the “euro-roll” type of longitudinal and transverse seams of the packaging;
Unit for putting the date on the seam of the packaging (day, month, year “XX XX XX”);
Electronic control unit with light indication and monitoring of emergency situations.
Additional equipment:
Tube with collar (for changing the film width);
“Stand-up bag” formation unit;
Encoder (for pulling the film along the length of the package);
Thermal printer (from 6 characters, at any point of the package);
Seam punching device (“Euro-loop”, “Euro-cut”);
2nd level of dispenser (for hard-to-flow products);
Protective cover;
Compressor.
Equipment:
Electric drives – STM (Italy);
Pneumatic drives – CAMOZZI (Italy);
BU – MiKra (Ukraine);
Frequency converters – INVT, HYUNDAI (Korea);
Bearings – CX (Poland);
Product contact units – steel 304.
Possibilities: 600-2700 packs/hour.
Type of packaging: package (pillow/standing).
Products: bulk products.