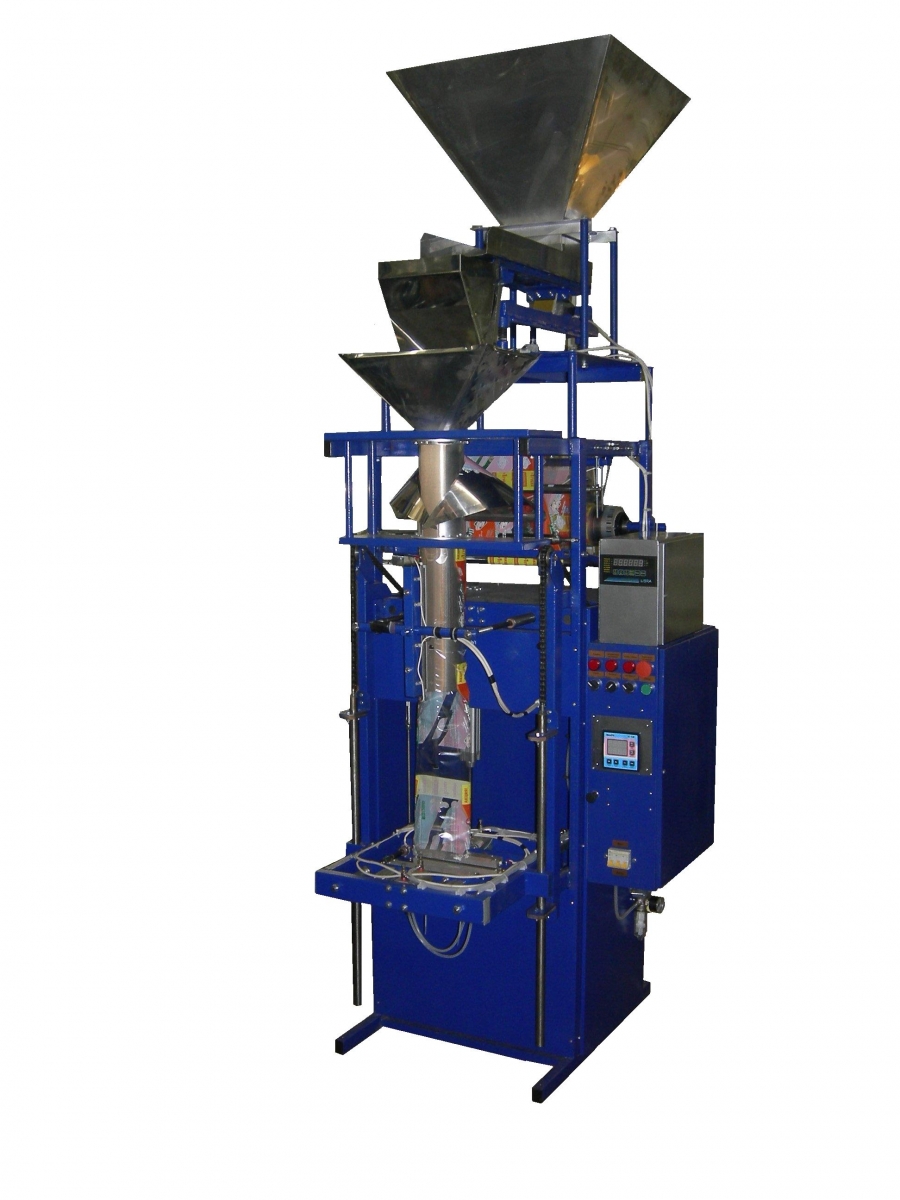
The filling and packaging machine has a pneumatic drive and is designed to organize a continuous cycle of weighing bulk products (cereals, nuts, coffee, crackers, chips, candies, cookies, granules) and packing them in polymer films (polypropylene, duplex, triplex). The machine is controlled by a controller, which allows to practically exclude human participation in the process of packaging products.
The filling and packaging machine consists of a packaging machine and a weighing electronic batcher.
The filling machine is universal (used for various types of bulk products), has the lowest price (among similar models of equipment), has the ability to change the size and characteristics of packaging materials.
Characteristics.
Power supply, V/Hz | 380/50 |
Electricity consumption, kW/hour | 1,5 |
Pneumatic supply**, atm./l.min. | 6/250 |
Length/Width/Height (not more than), mm | 1700/1200/3100 |
Weight (not more than), kg | 360 |
Film roll width/diameter (max), mm | 380/300 |
Productivity (max.)*, packs/hour | 500-2000 |
Volume of storage bin, l | 60-240 |
Dosage range, g | 20 – 1000 (до 2000 – под заказ) |
L/W of package (max), mm | 300/180 |
* The equipment performance depends on the dose weight, product properties, packaging material properties, and packaging length.
** To ensure the operation of the pneumatic drives of this packaging machine, a “compressor” (supplied separately) is required.
Description of work.
The product to be packaged is poured into the hopper of the electronic weigh batcher, from which it is fed by means of a vibrating tray into the weighing bucket suspended on a strain gauge. When the bucket is filled to the specified weight parameters, the strain gauge sends a signal to the electronic control unit of the batcher, which stops the vibrating tray, ceasing the product feed.
When receiving an impulse from the packaging machine (the “Unloading” signal), the controller sends a signal to open the weighing bucket, the bucket opens, pouring its contents into the funnel. Through the funnel, through the tube of the sleeve-forming device, the product is poured into a rolled-up tube of packaging film with a sealed back seam and bottom (packaging blank). At this time, the controller turns on the vibrating tray to fill the weighing bucket with the next portion of the product.
The operation of the packaging machine is controlled by its own control unit, which includes a microcontroller and is synchronized with the weigh batcher controller via an electrical connection. The microcontroller uses pneumatic drives to activate the soldering unit of the equipment.
The soldering unit of the packaging machine uses the principle of constant heating and simultaneously seals the top seam of the filled package, the bottom and side seams of the next package with a “euro-roll” type of seam in one go. At the same time, at the moment of welding the film, the soldering unit shifts downwards by the set length of the package, thereby pulling the packaging film. Considering that the package is welded directly on the film web, when it is pulled, the roll is unwound and the film is rolled up, using a special collar, into a tube around the tube, i.e. a blank for the next package is formed. The length of the pull and, accordingly, the length of the package are controlled by a photo mark applied to the film, or mechanically (by adjusting the height of the sensor).
When the bottom point is reached, the filled package is separated by cutting the film with a mechanical serrated knife. At the same time, the microcontroller of the packaging machine sends a pulse (the “Unloading” signal) to the weigh batcher controller, filling the next package, unclamps the welding elements of the soldering unit and moves them upward to seal the next seams. The cut-off package falls on the floor, into a special container (box) or onto a discharge conveyor (supplied separately).
Additionally, the microcontroller monitors the moments of emptying the weigh batcher hopper, the end of the roll of packaging material and other emergency situations.
Peculiarities.
The packaging machine is ideal for packaging products of any flowability (seeds, buckwheat, rice, millet, peas, sugar, salt, pasta, chips, candies, cookies, crackers, coffee, tea, etc.), with the exception of highly dusty products (flour, powdered sugar). Taking into account the dosing method and the characteristics of the weighing batcher, the packaging machine allows you to arbitrarily change the portions of the packaged product, as well as achieve the most accurate dosage. Unlike the machine with a volumetric batcher (AF-35-OM), it has no restrictions on changing the packaged product.
The packaging machine has significant dimensions and weight and requires floor placement. There are also restrictions on the width of the film used and the height of the formed package, specified in the technical specifications. It is possible to manufacture a machine of increased dimensions – the maximum film width will be up to 500 mm, and the height of the package up to 400 mm.
This packaging equipment is available in the following models: AF-35-V1, AF-35-V2, AF-35-V3, AF-35-V4. The difference between them is in the number of weighing buckets (“streams”): in AF-35-V1 – 1 “stream”, with a capacity of up to 500 packages/hour, and in AF-35-V4, respectively, 4 “streams”, with a capacity of up to 2,000 packages/hour.
Equipment.
Standard equipment:
Electronic weighing 1-4 flow dispenser with a storage bin;
Former of 3-seam “pillow” – collar packaging (up to 380 mm);
Automatic carriage system for pulling packaging material along the length and along the “photo mark”;
Sealing unit of the “euro-roller” type of longitudinal and transverse seams of the packaging;
Unit for putting the date on the seam of the packaging (day, month, year “XX XX XX”);
Electronic control unit with light indication and monitoring of emergency situations.
Additional equipment:
Tube with collar (for changing the film width);
Stand-up bag forming unit;
Thermal printer (from 6 characters, at any point of the package);
Seam punching device (“Euro loop”, “Euro punching”);
2nd level of dispenser (for hard-to-flow products);
Protective cover;
Compressor.
Equipment:
Electric drives – STM (Italy);
Pneumatic drives – CAMOZZI (Italy);
BU – MiKra (Ukraine);
Frequency converters – INVT, HYUNDAI (Korea);
Bearings – CX (Poland);
Product contact units – steel 304.
Possibilities: 500-2000 packs/hour.
Type of packaging: package (pillow/standing).
Products: bulk products.