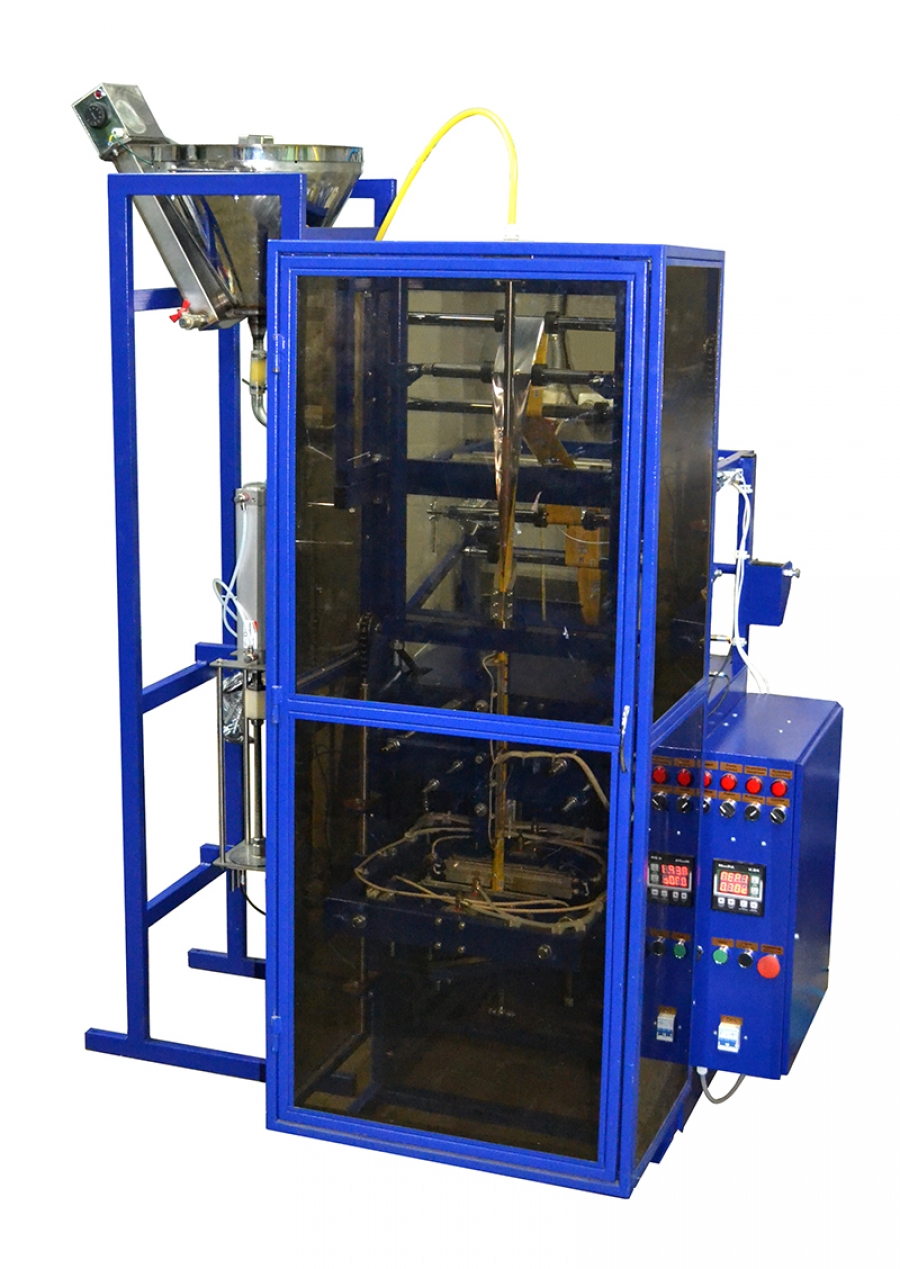
The filling and packaging machine is designed for a continuous cycle of volumetric dosing of liquid and pasty products (honey, condensed milk, liquid oil, shampoo) and their packaging in stick-type packages made of polymer films (laminated paper, duplex, triplex).
Consists of a pneumatic packaging machine and a liquid piston dispenser.
The filling and packaging machine is used for volumetric filling and packaging of flowing products, and in various modifications of this model, it allows dosing products from 1 to 20 cm3, as well as using stick packaging from 17 to 25 mm.
Characteristics.
Power supply, V/Hz | 220 / 50 |
Electricity consumption, kW/hour | 1,5 |
Pneumatic supply**, atm./l.min. | 6/400 |
Length/Width/Height (not more than), mm | 1100/ 1200/ 1800 |
Weight (not more than), kg | 300 |
Film roll width/diameter (max), mm | 250 / 300 |
Productivity (max.)*, packs/hour | 1200-4800 |
L/W of package (max), mm | 200 / 17(24) |
Dosage range, cm3 | 1-20 |
* The equipment performance depends on the dose volume, the properties of the packaged product, the properties of the packaging material and the length of the package.
** To ensure the operation of the pneumatic drives of this packaging machine, a compressor is required (not included in the basic package).
Description of work.
The suction pipe (silicone hose) of the liquid dispenser is inserted into a container with the liquid being filled, from where it is taken for dosing. The containers can be arbitrary and are used exclusively according to the operator’s needs and the length of the suction pipe. Upon receiving a signal from the electronic control unit of the packaging machine, the pneumatic drives of the liquid dispenser pull the rod out of the measuring piston cylinder. As a result of the vacuum, the liquid being dosed moves into the measuring cylinder along the suction pipe. The dose volume is regulated by a mechanical regulator, along the length of the cylinder rod movement.
Upon reaching the end point (the lower position of the measuring cylinder rod), the electronic control unit sends a signal to switch the pneumatic drives to reverse motion, pressing the rod into the measuring cylinder and compressing the liquid being dosed inside it. When compressed, the liquid that has filled the filling cylinder is squeezed out through the dispensing branch pipe located in the tube on which, using a collar, the packaging film is rolled up into a sleeve with a sealed rear longitudinal seam and lower horizontal seam (stick pack). After dispensing a dose of the packaged product, the control unit again sends a signal to the pneumatic drives to pull out the rod, and activates the sealing unit. The sealing unit of this packaging equipment uses the principle of constant heating of the packaging film and seals the upper seam of the product-filled package and the rear longitudinal seams of the next stick package with a “euro-roller” type of seam. At the same time, at the moment of sealing (closing of the heaters in the horizontal position), the horizontal heating pads of the sealing unit (carriage) are shifted downwards by the set length of the package. Since the sealing pads move downwards without unclenching, they pull the packaging film along with them. The roll of packaging material is unwound, divided into streams by a disk knife, and the future stick packaging is formed using collars.
When the sealing unit reaches the bottom, the filled stick packaging is separated by cutting the film with a mechanical serrated or straight knife. At the same time, the rod is pressed into the measuring cylinder and the next dose of liquid is dispensed into a new stick package, after which the electronic control unit sends a signal to release the horizontal sealing pads and moves them up to seal the next stick package. The cut package falls on the floor, into a special container (box) or onto a discharge conveyor.
A microcontroller is installed in the electronic control unit of the packing machine, which monitors emergency situations in the packer’s operation: the end or rupture of the roll of packaging material, pinching of the portion, etc.
Peculiarities.
The filling machine with a liquid volumetric dispenser is optimal for portion filling and packaging in 3-seam stick packaging of liquids and pasty products, such as: water, juice, perfumes, medicines, ketchup, mayonnaise, oil, liquid soap. Stick packages are optimal for use in most cafes, restaurants, gas stations and other catering establishments.
This packaging equipment is used in floor placement. The installation has restrictions on the width of the film used and the height of the formed stick package, specified in the technical specifications section. It is possible to manufacture a filling and packaging machine of increased dimensions, according to individual customer solutions (calculated individually).
The filling machine is available in models AF-120-G1, AF-120-G2, AF-120-G3, AF-120-G4. The machines differ in the number of “streams” of the dispenser and packaging film, which helps to increase the productivity of this equipment: in the AF-120-G1 – 1 “stream” of liquid dispenser and 1 stream of packaging material, with a productivity of up to 1200 packages/hour, and in the AF-120-G4, respectively, 4 “streams” of liquid dispenser and 4 streams of packaging material, with a productivity of up to 4800 packages/hour.
Equipment.
Standard equipment:
Volumetric piston (1-4 flow) liquid dispenser;
Former (1-4 flow) of “stick” packaging;
Automatic carriage system for pulling packaging along the length and along the “photo mark”;
Sealing unit for longitudinal and transverse seams of packaging;
Electronic control unit with light indication and monitoring of emergency situations.
Additional equipment:
Discharge conveyor;
Receiving storage bin with heating;
Thermal printer (from 6 characters, at any point in the package);
System for monitoring the length of the package by the pattern on the film;
Device for applying a notch to the seam;
Protective cover;
Compressor.
Equipment:
Electric drives – STM (Italy);
Pneumatic drives – CAMOZZI (Italy);
Used – Libra, MiKra (Ukraine);
Frequency converters – INVT, HYUNDAI (Korea);
Product contact units – 304 steel.
Possibilities: 1200-4800 packs/hour.
Type of packaging: stick pack.
Products: liquids and pastes.